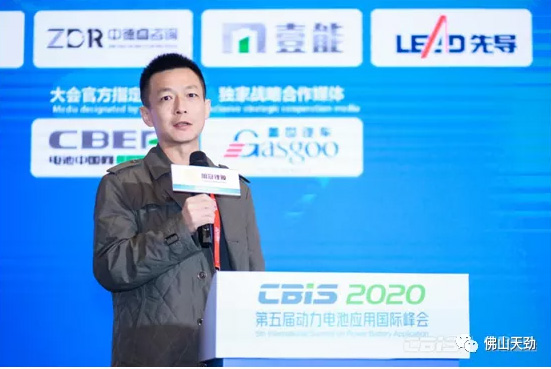
▲The picture shows Dr. Wang Qiang, CTO of Teamgiant new energy and President of the Research Institute, giving a speech on the stage
On October 16, 2020, the power battery and industry chain heavyweight industry grand gathering - "the fifth power battery application International Summit (cbis2020) and the first China new energy and new materials (Ningde) summit" was opened. At the theme forum 2, Dr. Wang Qiang, CTO of Teamgiant New Energy Technology Co., Ltd. and President of the Research Institute, delivered a special speech entitled "thinking on the path of solid state battery industry".
Dr. Wang Qiang said: the title of my report is mainly divided into four parts. The first part is a brief introduction of solid-state batteries; the second is research ideas; the third is solutions; and the fourth is a little bit of research results that have been achieved.
Solid state battery, I don't want to talk about it, because there are a lot of researches on solid-state battery in the industry. I just want to talk about it. At present, Teamgiant new energy mainly focuses on soft package power, so the basic conditions for solid-state battery are a little better than those of square or cylinder, so this place talks more about the implementation path of soft package. There are some common problems with solid-state batteries: the first is the low ionic conductivity of solid-state electrolyte; the second is the lack of visible and quantitative means of solid-state interface; the third is that the whole manufacturing process of solid-state batteries has greatly subverted the industry. Therefore, is there a simpler and more mature way to do this? We will talk about it below.
At present, the development level of batteries in the whole industry may be mentioned that they will develop to 400wh / kg or 500wh / kg in the future. However, considering the current situation of material reserves, the initial mass production of solid-state batteries from 300wh / kg to 350wh / kg can be realized. I think it may be a little larger in two to three years. The whole idea of our place, in line with the solid electrolyte, adopts in-situ polymerization and precise solidification, which is more compatible with the existing power production line process, which is the basic idea to realize at present. The second current positive electrode uses high nickel and negative electrode uses silicon oxygen. The latter one is jointly developed with the Chinese Academy of Sciences, which will be briefly discussed later.
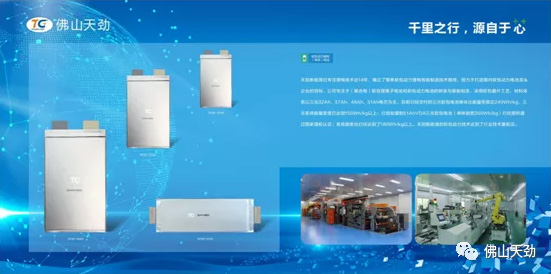
In fact, the solid electrolyte in this case is the solid electrolyte of polymer, which is different from the traditional sulfide or oxide solid electrolyte. I feel that polymer electrolytes will still have a faster industrialization speed in recent years, because the first way it uses is small molecules, the second is ionic liquids, and the third is plasticizer. There are many ways to achieve this. At present, Teamgiant new energy adopts the method of in-situ polymerization. At the level of soft package, we add precursor solution and heat initiated polymerization to achieve this method. The whole production line, including the whole operation mode, the adjustment range of the whole soft package process is very small. We do power batteries. At present, there are many ways to prevent thermal runaway in the industry. For example, there are cloud flakes. In fact, pack has many aspects to prevent thermal runaway. Whether there are endogenous factors in the cell thermal runaway, this is the current realization way of the whole process. At present, the trial conclusion is more suitable for large-scale mass production, here we talk about the preliminary performance. We have made a lot of attempts in the whole coating process, including polymerization process, and many parameter variables have been optimized. Now the industry has some concerns about ncm811 or NCA. In this way, we may implant some thermal runaway solutions into the cell. In fact, there is a very special point. The existing national standards can meet the requirements, and even the performance of national standards for safety testing is better than that of ncm622 or ncm523. Because ncm811 has a very special overshoot ability, it will be found that whether ncm811 or NCA, it is more about how to prevent and control the thermal runaway, rather than the national standard test requirements.
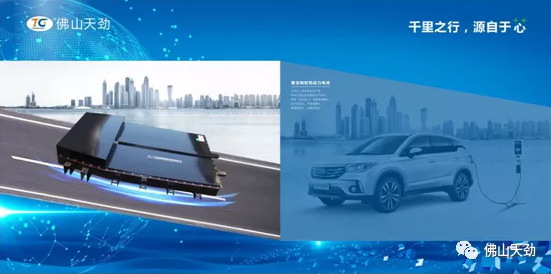
This is our general idea. At present, the ring opening polymerization of DOL initiated by lithium salt is adopted. The polymerization temperature is about 50-60 ℃, which is close to the aging temperature of the whole process of soft package. The whole basic principle is not discussed in this part, because it is only considering the current references, including the preliminary conclusions of some research institutes, this dol was initially selected for ring opening polymerization.
This is something that has been done at present. In fact, it will be found that dol of 60 degree thermal polymerization has the characteristics of polymer or polymer, because there is no plasticizer, including other additives, so the ionic conductivity is lower. It can be seen that the ionic conductivity is very close to the requirements of the electrolyte that can be used at present. Because we prefer pure electric power battery in the whole application, the whole rate requirements, including the requirements of the whole energy density, are relatively within a controllable range, so the performance of the whole test will be seen later. It should be emphasized that the diaphragm will exist in the whole process, including the ceramic coating, but there are some changes during the injection. Whether it is just mentioned that the aluminum plastic film, including the diaphragm, including ceramic coating, including conventional positive and negative electrode materials, adopts the in-situ method.
This is a device developed together with scientific research institutes. It mainly solves the problem of in-situ characterization of the stress in the process of solid-state battery or semi-solid battery and the contact between electrode and electrolyte. Because it can be found that the in-situ stress can be used to monitor the current contact stress of the solid electrolyte between the cathode material and the electrolyte in real time when the battery is charged and replaced, or when a voltage window is limited, or when the test is carried out at different temperatures. In fact, we have a lot of data behind us, but we have not fully developed it in this area, because today we will focus on more ideas Point.
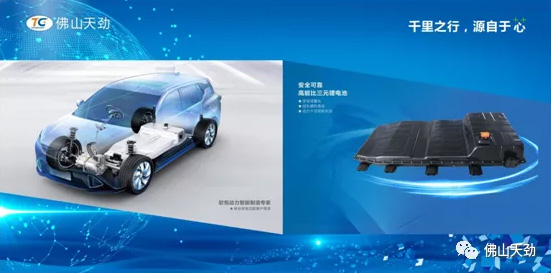
Dr. Wang Qiang believes that the current solid-state battery manufacturing is relatively the most core. No matter whether the lithium metal will be made in the future, or the graphite and silicon oxygen will be used in the same range. This system is more applicable. Ppt said above is composite lithium, its own enterprises do research and development or cooperate with universities, metal lithium use a little more. At present, the method used is graphite plus a small amount of silicon oxygen, with high-power positive electrode for synchronous and accurate solidification, using the existing soft package production process. This is a preliminary performance at present. This is the first product. At present, the energy density is about 277wh / kg, and the volume is 568wh / L. there is still room for optimization of the overall cycle life. It is only said that the process parameters of the current solid-state battery or in-situ polymerization need to be further optimized.
This is the second product with an energy density of 302wh / kg, which is combined with silicon oxide and graphite. The whole cycle performance is not particularly excellent at present, because it has something to do with the introduction of current solid electrolyte. If the conventional liquid electrolyte is used, the cycle life will be a little better than this one, which is something that needs to be improved in the future. As mentioned just now, let's emphasize again that the final starting point for us to do this is to implant a key component or a component inside the battery that can prevent the battery from losing control of heat or thermal diffusion. This is different from the original liquid electrolyte method. This is also in addition to the industry development, more from the pack level to prevent and control thermal runaway or thermal diffusion. We are still exploring whether it is possible to do such a thing inside the battery and hope to get your criticism and correction.
Just after the cell came out, in fact, we are also thinking that the innovation ability of pack in the industry this year is still very large. Whether it is blade battery or CTP, it seems that this method is difficult to realize CTP for soft package, and CTC may be more difficult. As a supplier of soft package power, in fact, we are also thinking about whether there is a chance to do so in the future. For example, if the energy density of the cell has not been greatly improved, we will have the opportunity to do some lightweight or improve the energy density of the system like a square. At present, we still try to make the module bigger. We can see that the whole way adopts the pack mode of plastic frame. This page shows the final form of the battery pack for battery replacement. The final composition of the battery pack standard box is composed of four standard boxes, each of which has 15 kilowatts of electricity. It is used in logistics vehicles or passenger cars. The standard matching power is 60kwh. This is also a battery pack that is currently cooperating with a company in Hangzhou. Therefore, during the whole process, we can see that there are only two modules in a standard box. The large frame and the overall glue pouring method are adopted. There are many hollow structures on the top, which are filled with flame retardant glue and have heat conduction parameters inside.
In general, the hope of power battery is not only from the level of pack, but also from the level of battery cell to think about the future development of battery industry. Because now, because our own industry has developed to the present, it has slowly returned to the original state of lithium iron phosphate. We can see that many commercial vehicles and some passenger cars are slowly turning back to the state of lithium iron. Is there no future for Sanyuan? In fact, I think the technology is still making progress. Maybe in the next 1 to 2 years, there will be a big breakthrough in the aspect of ternary security. At this time, the path of the whole industry or the research direction of the whole industry will have a relatively big change. Lithium iron phosphate is a very good way, but I think we should make concerted efforts to make progress together in the ternary system.
Thank you!